GM Boosts Indiana Car Production Amid Tariff Impact
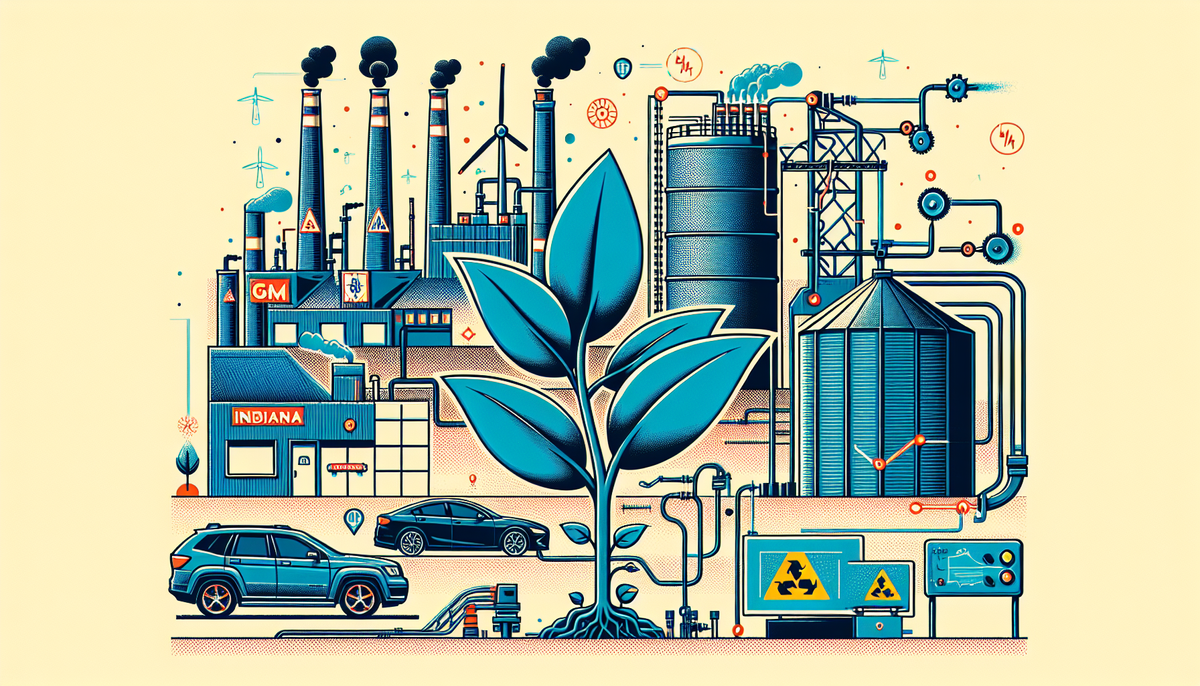
GM’s Strategic Production Surge in Indiana
General Motors (GM) has recently announced a significant ramp up in its vehicle production at its Indiana facility. This bold move comes in response to President Trump’s imposition of a 25% tariff on all foreign-made cars and auto parts, a policy designed to revitalize domestic manufacturing and protect national economic interests. GM’s decision to increase production at its Fort Wayne plant is a strategic adjustment to support current manufacturing needs and limit the reliance on imported components, a response expected to impact both the industry and consumers alike.
Context and Economic Implications
The imposition of tariffs, branded as a move to let the industry 'flourish like never before,' has forced GM and other automakers to rethink their production strategies. The tariffs, originally set to go into effect on April 2 during a period labeled as 'Liberation Day,' were intended to protect American jobs and promote reshoring of production. However, the policy has had mixed consequences.
Key economic implications include:
- Job Creation: GM has announced plans to hire several hundred temporary workers at its Fort Wayne plant. This sudden creation of jobs is anticipated to benefit the local economy and reduce unemployment in the region.
- Supply Chain Realignment: With tariffs affecting the cost and availability of imported auto parts, companies like GM are focusing on bolstering domestic production of critical components.
- Consumer Price Impact: Although the drive to manufacture more locally could stabilize supply chains, there is a risk that increased production costs will eventually be passed on to consumers, potentially leading to higher vehicle prices.
Operational Adjustments at the Fort Wayne Plant
In order to implement these strategic changes, GM has scheduled a temporary shutdown of its production line at the Fort Wayne assembly plant from April 22 to 25. This brief pause in production is essential to reconfigure assembly processes, integrate new operational protocols, and ensure compliance with the evolving market demands brought about by the imposed tariffs.
The production upgrade at the Fort Wayne plant involves several critical steps:
- Expanding the Workforce: By bringing in several hundred temporary workers, GM aims to quickly scale up its production capacity. This is expected to streamline the manufacturing process and fill the gaps left by disrupted supply channels.
- Restructuring the Assembly Line: The brief stoppage is being used to implement operational adjustments that will better accommodate the new production demands, ensuring both efficiency and quality in the output of popular models like the Chevrolet Silverado and GMC Sierra.
- Enhancing Domestic Sourcing: The company is also reassessing its supplier network, placing greater emphasis on sourcing components from American manufacturers. This shift is in line with the tariffs’ objective of reducing dependence on foreign parts.
Impact of Tariffs on the Auto Industry
The current tariff policy presents both opportunities and challenges for the automotive sector. On one hand, the tariffs have encouraged reshoring—a phenomenon supported by research from global management consulting firm McKinsey & Company—which in previous decades has led to significant job creation and an uptick in domestic production.
On the other hand, studies by the Federal Reserve Bank of New York have highlighted the negative effects of similar policies, documenting instances where stock market responses and firm equity values have suffered on tariff announcement days. In the case of GM, the immediate reaction was evident as investor confidence faltered, leading to a notable dip in the company’s shares.
Industry and Market Reactions
Following the tariff announcement, GM’s share price experienced a significant drop—more than seven percent at one point—reflecting investor anxiety over the ramifications of increased production costs and disrupted international supply chains. This decline was compounded by concerns regarding GM’s operations in Canada and Mexico, where production had been flourishing under previous trade dynamics.
Reactions among market analysts have been varied:
- The Optimists: Proponents of GM's decision argue that increasing domestic production will ultimately solidify the company’s market position by reducing vulnerable dependencies on imported parts and aligning production processes with national economic strategies.
- The Skeptics: Critics caution that while tariff-driven reshoring may benefit production metrics in the short term, it is likely to result in elevated costs for end consumers, as manufacturers pass some of the increased expense along the supply chain.
Broader Implications for the U.S. Economy
GM’s strategy represents more than just an isolated case; it is indicative of a broader trend within American industry aimed at reestablishing the country’s manufacturing prowess. Several far-reaching implications can be drawn from this shift:
- Reshoring of Manufacturing: Increasing domestic production is part of a growing movement among American companies to relocate manufacturing operations back onshore. This trend is seen as a way to safeguard against unpredictable international trade policies and to stimulate local economies.
- Transformation of the Labor Market: The creation of temporary positions at facilities such as the Fort Wayne plant may lead to more permanent job growth over time, contributing to a dynamic labor market that is better equipped to handle future economic challenges.
- Consumer Costs and Market Dynamics: There is an inherent tension between the benefits of reshoring and the potential rise in consumer prices. As manufacturers incur higher costs from domestic sourcing, these increased expenses could be mirrored in the retail prices of vehicles, influencing purchasing decisions nationwide.
Expert Opinions and Future Outlook
Experts across various fields have weighed in on GM’s move, underlining its significance in the context of modern manufacturing practices. Dr. Martin Ellis, an economist at the University of Michigan, observed, "GM's recalibration of its production strategy is emblematic of how traditional manufacturing sectors must evolve in response to both political and economic pressures. While tariffs can provide short-term advantages, the long-term success of such strategies will depend on how well companies manage cost efficiency and supply chain stability."
The future remains uncertain, however. As international trade policies continue to evolve, companies like GM will have to remain agile, modifying strategies as new challenges emerge. Historical data indicates that while tariff policies can catalyze domestic growth, they also necessitate careful planning to avoid adverse economic repercussions such as price hikes and reduced consumer spending.
Comparative Analysis: U.S. Versus Global Production Practices
A comparison between GM’s approach and the production practices of its global competitors reveals several noteworthy contrasts. Internationally, companies that have diversified supplier bases and localized production lines tend to experience fewer disruptions when faced with tariff challenges. In contrast, firms that have heavily relied on global supply chains are finding it more difficult to adapt quickly.
Some of the key comparative insights include:
- Supply Chain Versatility: Companies with a robust and diversified sourcing strategy are better positioned to mitigate the sudden shocks of new tariff policies.
- Local vs. Global Production: Firms that already emphasize local production are less vulnerable to international trade fluctuations, thereby maintaining more consistent pricing and production levels.
- Adaptability: The ability to quickly pivot production strategies is crucial. Agile companies can reconfigure their operations in response to policy changes far more effectively than those with rigid international structures.
Historical Perspective on Tariff Policies in the U.S.
Tariff policies have long been a tool for safeguarding domestic industries and redirecting economic activity. The current situation echoes historical instances when the U.S. government introduced tariffs to stimulate local production and protect emerging industries. Over the decades, these policies have had a transformative impact on manufacturing—both by bolstering local production and by prompting significant shifts in international trade pathways.
For readers interested in exploring the historical context further, reputable sources such as the Federal Reserve and detailed studies by economic research institutions provide extensive insights into how tariffs have reshaped the landscape of American manufacturing over time.
The Road Ahead: Prospects and Challenges
Looking forward, GM’s enhanced focus on domestic production presents both significant prospects and formidable challenges. Among the prospects:
- Increased Domestic Production: A shift towards reshoring manufacturing offers the potential for a more resilient and self-sufficient industrial base.
- Economic Revitalization: The ripple effects of job creation and localized manufacturing may contribute positively to regional economies, particularly in industrial hubs like Indiana.
- Long-term Competitiveness: By reducing dependency on volatile international supply chains, companies like GM could improve their long-term competitiveness in global markets.
However, several challenges warrant close attention:
- Managing Higher Costs: The increased production costs inherent in domestic manufacturing could result in higher retail prices, potentially dampening consumer demand.
- Achieving Supply Chain Stability: Shifting away from international suppliers requires building new relationships with domestic vendors, a process that may involve initial inefficiencies and growing pains.
- Regulatory and Market Uncertainty: As trade policies continue to evolve, manufacturers will need to remain nimble and ready to adapt to further regulatory shifts.
Conclusion
GM’s decision to dramatically increase vehicle production in Indiana represents a watershed moment in U.S. automotive manufacturing. It encapsulates the complex interplay between government policy, economic strategy, and operational resilience in a rapidly changing global landscape. While the immediate impacts include job creation and a potential reshaping of supply chains, the long-term outcomes will depend on how well GM and its peers manage cost pressures and adapt to evolving trade policies.
To gain additional insights and track further developments, readers are encouraged to consult authoritative sources such as Reuters, the Federal Reserve, and economic analyses by institutions like McKinsey & Company. As the narrative of reshoring and tariff-driven market adjustments continues to unfold, this strategic shift in production may well serve as a blueprint for the future of American manufacturing.
This in-depth analysis not only highlights the immediate operational changes at GM’s Fort Wayne plant but also provides a broader view of how domestic production strategies are evolving in the face of global economic challenges. By embracing these changes, GM is positioning itself to better withstand international trade shocks, ensuring that American consumers and the labor market gain from a more robust and competitive automotive industry.
Comments ()